Advancing Multi-Axis Additive Manufacturing: Generalized Inverse Kinematics
Researcher: Zahra Faghihrasoul
As additive manufacturing technology evolves, multi-axis 3D printers are emerging as the new frontier, offering enhanced precision, speed, and capability. However, these advancements also introduce complex challenges in motion control, path planning, and real-time decision-making. the Multi-Axis Additive Planning research of
design lab is tackling both computational geometry conformal slicing:
quadric slicing,
non-planner toolpaths(DLG),
concavity planning to avoid collision and
variable density infill. My research focuses on developing a universal inverse kinematic framework that bridges the gap between geometric modeling and machine execution. This involves the machines' motion planning by generating G-codes with additive manufacturing consideration.
Traditional 3D printers operate layer-by-layer and struggle with overhangs, stepping effect, and mechanical anisotropy. Multi-axis printing overcomes these issues, unlocking:
-
Complex geometry fabrication without support structures
-
Improved mechanical performance and directional strength
-
Time and material savings
-
Potential for in-place repair and hybrid manufacturing
However, this leap forward is not without its challenges. Avoid collision, smooth and consistent motion of the tool, collaboration between the speed of the tool and the material extrusion. Generating reliable machine motion requires solving nonlinear inverse kinematics in real time. while the effort is to bring precision, smoothness and universality to the application. The focus is to present a generalizable inverse kinematic method designed for diverse multi-axis machine configurations, that supports an arbitrary combination of revolute and prismatic joints.
My contribution is to design the control system to bring the computation geometry tool in into machine motion planning through a versatile, symbolic, and optimization-driven kinematics pipeline.
Key Contributions So Far:
-
URDF-to-DH Conversion Pipeline: Automatically converts machine description (URDF format) into Denavit–Hartenberg parameters and symbolic kinematic equations.
-
Levenberg-Marquardt Optimization: Minimizes an additive-manufacturing-specific objective function combining spatial precision and surface alignment.
-
Universal G-code Generator: Outputs custom G-code based on machine geometry and surface normal, tailored to 5- and 6-axis systems.
-
Flexible Machine Compatibility: Supports arbitrary combinations of revolution and prismatic joints, enables widespread applicability.
-
Demonstration on Complex Surfaces: Validated through path-following on spherical geometries to demonstrate precision, reachability, and stability.
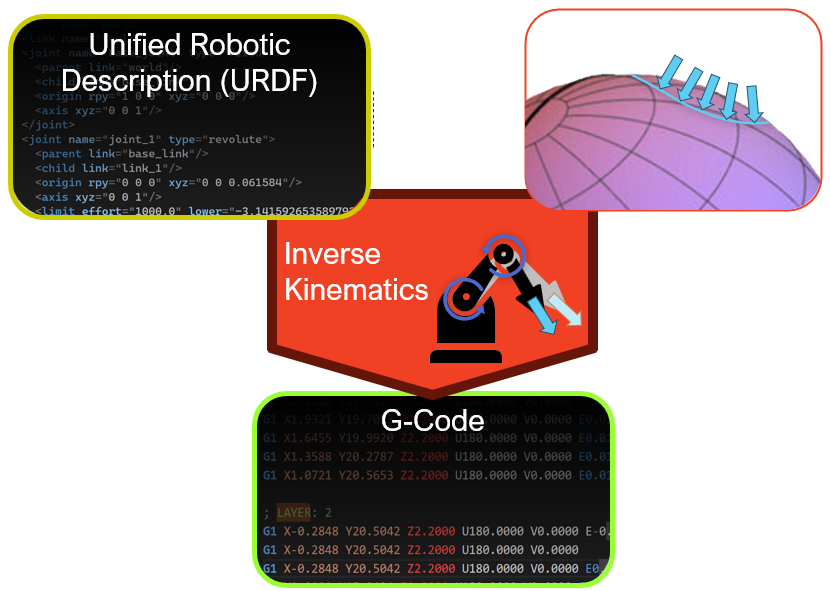
More information is available on a Paper that its pre-print version is available by request.
Connect With Us
We’re looking for collaborators and sponsors who want to shape the next generation of additive manufacturing system.
Primary Researcher:
Zahra Faghihrasoul, PhD Student. Graduation June 2026
Advisor:
Dr. Matt Campbell